一、模板與PCB的分離速度與分離距離(Snap-off)
絲印完后,
PCB與絲印模板分開,將錫膏留在PCB上而不是絲印孔內(nèi) 。對于最細(xì)密絲印孔來說,錫膏可能會更容易粘附在孔壁上而不是焊盤上,模板的厚度很重要, 有兩個(gè)因素是有利的, 第一, 焊盤是一個(gè)連續(xù)的面積, 而絲孔內(nèi)壁大多數(shù)情況分為四面,有助于釋放錫膏; 第二,重力和與焊盤的粘附力一起, 在絲印和分離所花的 2~6 秒時(shí)間內(nèi),將錫膏拉出絲孔粘著于PCB上。為最大發(fā)揮這種有利的作用,可將分離延時(shí),開始時(shí)PCB分開較慢。 很多機(jī)器允許絲印后的延時(shí),工作臺下落的頭2~3 mm 行程速度可調(diào)慢。
二、印刷速度
印刷期間,刮板在印刷模板上的行進(jìn)速度是很重要的, 因?yàn)殄a膏需要時(shí)間來滾動和流入模孔內(nèi)。如果時(shí)間不夠,那么在刮板的行進(jìn)方向,錫膏在焊盤上將不平。 當(dāng)速度高于每秒20 mm 時(shí), 刮板可能在少于幾十毫秒的時(shí)間內(nèi)刮過小的???。
三、印刷壓力
印刷壓力須與刮板硬度協(xié)調(diào),如果壓力太小,刮板將刮不干凈模板上的錫膏,如果壓力太大,或刮板太軟,那么刮板將沉入模板上較大的孔內(nèi)將錫膏挖出。
四、壓力的經(jīng)驗(yàn)公式
在金屬模板上使用刮板, 為了得到正確的壓力, 開始時(shí)在每50 mm的刮板長度上施加1 kg 壓力,例如300 mm 的刮板施加6 kg 的壓力, 逐步減少壓力直到錫膏開始留在模板上刮不干凈,然后再增加1 kg 壓力。 在錫膏刮不干凈開始到刮板沉入絲孔內(nèi)挖出錫膏之間,應(yīng)該有1~2 kg的可接受范圍都可以到達(dá)好的絲印效果。
為了達(dá)到良好的印刷結(jié)果,必須有正確的錫膏材料(黏度、金屬含量、最大粉末尺寸和盡可能最低的助焊劑活性)、正確的工具(印刷機(jī)、模板和刮刀)和正確的工藝過程(良好的定位、清潔拭擦)的結(jié)合。根據(jù)不同的產(chǎn)品,在印刷程序中設(shè)置相應(yīng)的印刷工藝參數(shù),如工作溫度、工作壓力、刮刀速度、模板自動清潔周期等,同時(shí)要制定嚴(yán)格的工藝管理制定及工藝規(guī)程。
① 嚴(yán)格按照指定品牌在有效期內(nèi)使用焊膏,平日焊膏保存在冰箱中,使用前要求置于室溫6小時(shí)以上,之后方可開蓋使用,用后的焊膏單獨(dú)存放,再用時(shí)要確定品質(zhì)是否合格。
② 生產(chǎn)前操作者使用專用不銹鋼棒攪拌焊膏使其均勻,并定時(shí)用黏度測試儀對焊膏黏度進(jìn)行抽測。
③ 當(dāng)日當(dāng)班印刷首塊印刷析或設(shè)備調(diào)整后,要利用焊膏厚度測試儀對焊膏印刷厚度進(jìn)行測定,測試點(diǎn)選在印刷板測試面的上下,左右及中間等5點(diǎn),記錄數(shù)值,要求焊膏厚度范圍在模板厚度-10%-模板厚度+15%之間。
④ 生產(chǎn)過程中,對焊膏印刷質(zhì)量進(jìn)行100%檢驗(yàn),主要內(nèi)容為焊膏圖形是否完整、厚度是否均勻、是否有焊膏拉尖現(xiàn)象。
⑤ 當(dāng)班工作完成后按工藝要求清洗模板。
⑥在印刷實(shí)驗(yàn)或印刷失敗后,印制電路板上的焊膏要求用超聲波清洗設(shè)備進(jìn)行徹底清洗并晾干,或用酒精及用高壓氣清洗,以防止再次使用時(shí)由于板上殘留焊膏引起的回流焊后出現(xiàn)焊球等現(xiàn)象。
深圳宏力捷推薦服務(wù):PCB設(shè)計(jì)打樣 | PCB抄板打樣 | PCB打樣&批量生產(chǎn) | PCBA代工代料
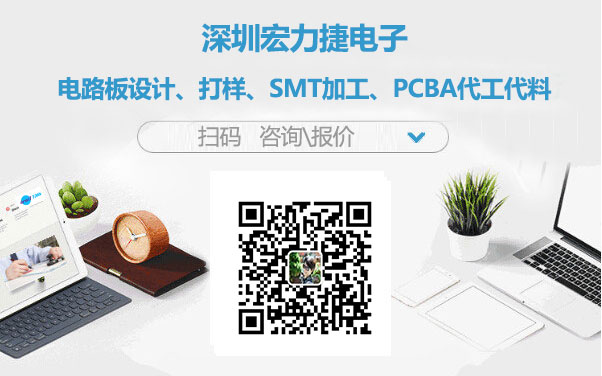